Recent prosecutions: Gate manufacturer fined £80,000 for multiple safety offences
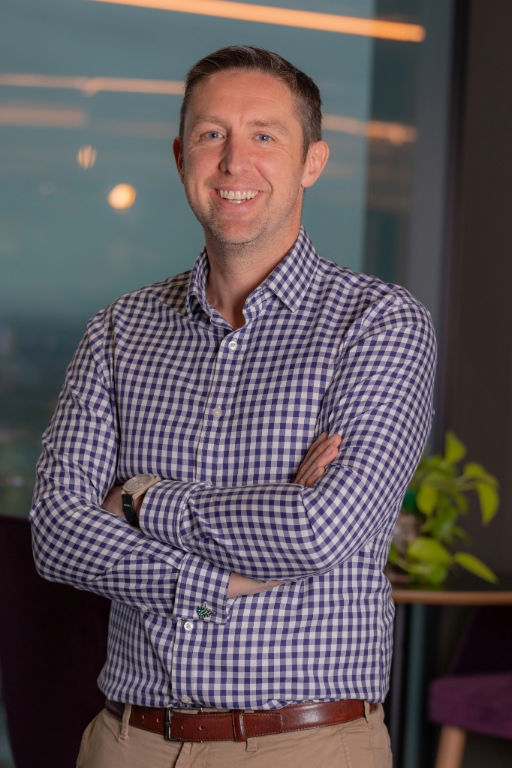
John Southall
July 11, 2025
3
min read
A gate manufacturing company that repeatedly failed to adhere to health and safety regulations has received a string of financial penalties, including £80,000 in fines, £7,495 in costs, and a £2,000 victim surcharge.
An initial visit from the Health and Safety Executive (HSE) found several serious safety breaches, including unsafe equipment, inadequate control of welding fume, and poor structural integrity in workplace areas. Inspectors issued a series of Improvement Notices requiring the business to:
- Take effective measures to control exposure to welding fume, a substance hazardous to health.
- Assess the structural safety of a mezzanine floor in use at the site.
- Examine lifting equipment, including a forklift truck, to ensure safe use.
The company also received a Notification of Contravention letter detailing a number of additional material breaches:
- Unguarded dangerous machinery parts.
- Inadequate edge protection on the mezzanine floor to prevent falls from height.
- Electrical systems not constructed to prevent danger, so far as reasonably practicable.
- Unsafe storage of flammable gases.
- No competent person appointed to assist with health and safety management.
Despite five follow-up inspections, three additional Improvement Notices, and a Prohibition Notice, the company’s poor safety practices continued to place employees, contractors and visitors at risk of serious harm. Even ducting installed above welding benches – intended to control exposure to dangerous fume – was supported by unstable and unsecured structures that were visibly bowing.
With standards falling well below legal requirements, the company was proactively prosecuted for failing to ensure the health, safety, and welfare of its employees and others affected by its work activities.
The HSE inspector said: ‘This prosecution follows a catalogue of failures, all of which posed serious risks to both the health and safety of workers and visitors of the site.
‘The company failed to implement basic, well-understood measures to control risks. Health and safety must be effectively managed – it’s not optional.’
Managing welding fumes at your builders merchant
According to HSE guidance, businesses must take effective measures to control exposure to hazardous substances such as welding fume.
The HSE accepts two forms of controls: respiratory protective equipment (RPE), which is usually hoods or masks, and local exhaust ventilation (LEV), which is typically overhead hoods, mobile vacuum units, or extractors that are intrinsically fitted to the welding equipment.
Both RPE and LEV require regular inspection. RPE should be checked monthly and records kept for 5 years. LEV should be checked every 14 months to remain compliant and working correctly, any workplace that carries out polishing or abrading should be tested every 6 months.
Protecting your team with RPE
When working with RPE, there are a few important areas to consider – from practicality to portability.
- Direct air-fed models are usually the most comfortable for the wearer. These can be fed either centrally by external air or via a battery-powered respirator, so consider how you’ll store and charge them.
- Fitted full or half masks can be hot and restrictive for staff who wear glasses, so they need to be face-fit tested.
- When using tight-fitting masks with filter cartridges, change the cartridge according to the manufacturer’s recommendations to eliminate harmful fumes.
Maximising LEV safety
Your LEV system removes fumes generated by the welding process, so regular suitability checks and accurate records are essential.
- Smoke matches and Draeger Tubes simplify detecting hazardous substances that could indicate equipment problems.
- Similarly, dust lamps set at angles of up to 120o can identify rogue fumes and help confirm your LEV system is working effectively.
- When using an overhead hood, mark out the extraction area with a clear line. This simple measure protects your team and demonstrates your safety commitment to inspectors.
Going the extra mile with health surveillance
To track workers’ long-term lung health, consider implementing a health surveillance programme wherever welding occurs.
All employees should have lung function testing and complete an annual health surveillance questionnaire. In addition, staff who regularly weld with metals containing respiratory sensitisers, such as nickel and chrome, should undergo asthma checks.
Questions about compliance? Ask the Opus team
To prevent prosecutions and keep your business consistently compliant, chat through your safety challenges with our experienced consultants.
Get in touch with the team on 0330 043 4015 or email hello@opus-safety.co.uk.
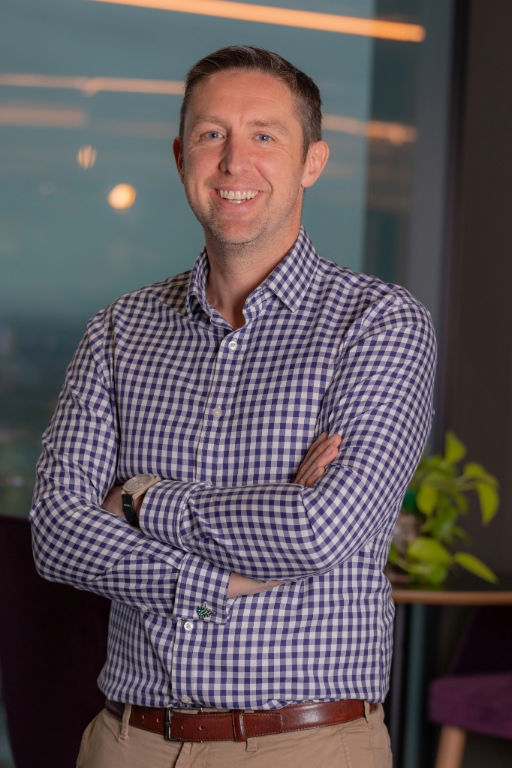
John Southall
July 11, 2025
3
min read